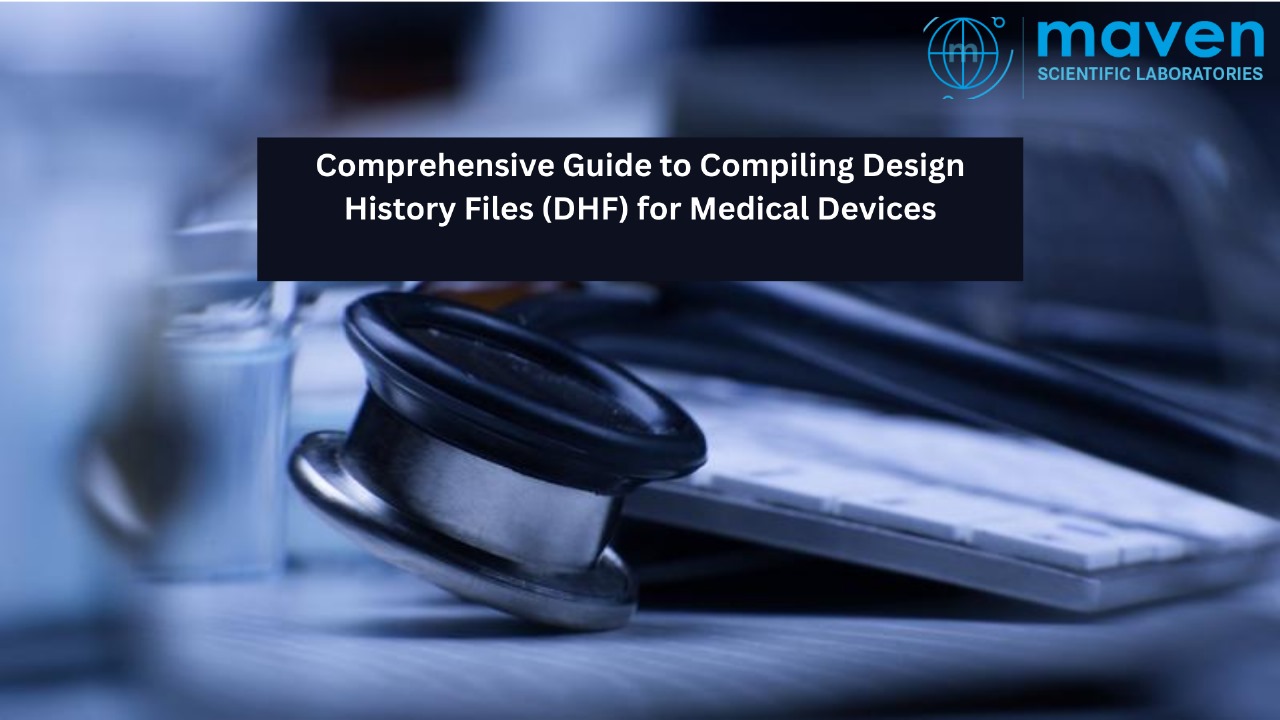
Comprehensive Guide To Compiling Design History Files (DHF) For Medical Devices
Understanding the Design History File (DHF)
The Design History File (DHF) is an essential element in the regulatory framework for medical devices, particularly under the Safe Medical Device Act. It serves as a comprehensive anthology of documentation and records that captures the "design history" of a finished medical device or product. This file is crucial for ensuring that the device was developed in a manner consistent with the approved design and regulatory requirements.
What Does a DHF Include?
A DHF typically encompasses:
Device Master Record (DMR): The DMR is a compilation of all the specifications, production processes, quality assurance procedures, and labeling and packaging requirements for the medical device.
Technical Documentation: This includes all the technical details, such as design specifications, drawings, and test data.
The Purpose of a DHF
The DHF is developed using a design control process, which is a systematic approach to managing product development activities. The file serves multiple purposes:
- Compliance: It ensures that the device meets all regulatory requirements.
- Traceability: It provides a clear trace of the design and development process, helping in case of audits or regulatory inspections.
- Quality Assurance: It aids in maintaining the quality and safety of the medical device throughout its lifecycle.
Common Challenges in Compiling a DHF
Despite its importance, creating and maintaining a DHF can be challenging for manufacturers and developers. Here are some of the common hurdles:
- Maintaining Paper Formats
- Accuracy and Completeness: The DHF needs to be meticulously maintained with accurate and up-to-date information. This includes ensuring that all documents are complete, properly signed, and stored securely.
- Document Control: Managing paper documents can be cumbersome, with risks of loss, damage, or misfiling. Transitioning to electronic document management systems can mitigate these risks but requires careful planning.
- Overloaded DHF
- Relevance: Avoid cluttering the DHF with irrelevant information like cost analysis, competitor studies, or other non-essential data. Focus on including only what is necessary for regulatory compliance and the safety and efficacy of the device.
- Disorganized Documentation
- Organizational Structure: Disorganization can lead to difficulties in retrieving necessary information, potentially causing delays in product approvals or even product recalls. It’s crucial to have a well-organized DHF where every document is easily accessible.
Key Components of Design Control Processes
The following design control processes are integral to compiling a compliant DHF:
- Design and Development Planning
- Purpose: Develop a clear plan that outlines the design and development process, including timelines, resources, and responsibilities.
- Design Input
- Process: Establish procedures to gather and document design input, ensuring that it addresses user needs and regulatory requirements.
- Design Output
- Documentation: Document the design output, which includes the specifications, drawings, and other relevant information that meets the design input requirements.
- Design Reviews
- Evaluation: Conduct regular design reviews to evaluate the progress and compliance of the design against the established plan.
- Design Verification
- Validation: Implement a validation process to ensure that the design output meets the design input requirements. This includes testing, simulation, and other verification activities.
- Design Transfer
- Specification Documentation: Document the transfer of design specifications to manufacturing, ensuring that all necessary information is conveyed accurately.
- Design Changes
- Change Management: Establish a process for managing and documenting design changes, ensuring that all changes are reviewed, approved, and incorporated into the DHF.
Best Practices for Compiling a DHF
To ensure your DHF is compliant and up-to-date, follow these best practices:
- Keep the DHF Updated: Regularly update the DHF to reflect any changes in design, processes, or regulatory requirements.
- Avoid Overloading: Stick to including relevant information only, avoiding unnecessary data that can clutter the file.
- Seek Expert Advice: Consult with seasoned regulatory experts to ensure that your DHF meets all necessary requirements and is well-organized.
Conclusion
Compiling a DHF is a critical process for medical device manufacturers. By understanding the components and challenges, and by following best practices, you can create a DHF that not only meets regulatory requirements but also supports the overall quality and safety of your medical device. Remember, a well-organized and up-to-date DHF is key to avoiding regulatory alerts and ensuring a smooth product approval process.
If you need assistance with compiling your DHF or navigating regulatory challenges, consider consulting with regulatory experts who can provide guidance tailored to your specific needs.